As the founder of Axis Solutions, I've seen firsthand how operational challenges in metal fabrication weave through the industry's very fabric. Tackling these challenges is not just about survival; it's about thriving in a space where efficiency, revenue, and profitability intersect. The metal fabrication industry faces an array of hurdles, including global supply chain disruptions, a perpetually widening skilled labor shortage, and the rising costs of materials—all while navigating increasing customer demands for speed and customization.
Few metal fabrication businesses are equipped with adequate systems to foster external collaboration or product design assistance, which can intensify the squeeze on margins. Against this backdrop, I believe that innovative approaches and technology adoption are non-negotiable for maintaining a competitive edge. This is particularly true when meeting unique customer specifications on design-to-order projects and addressing the skills gap on the production floor. The strategic integration of ERP systems, CAD technology, and rigorous training programs has proven indispensable in streamlining operations from procurement to the hands-on stages of production.
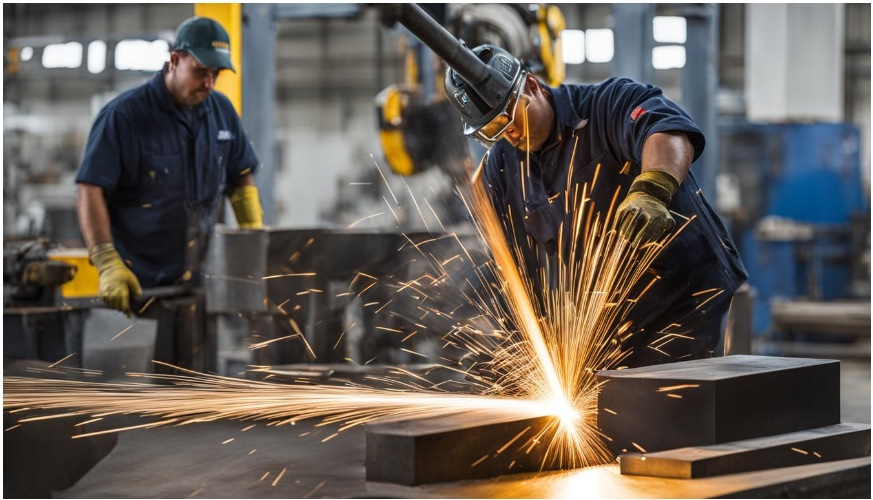
Create an image that showcases the difficulties and complexities of working with metal in a fabrication context. Use visuals that depict the equipment, tools, and materials that are commonly used in metal fabrication, highlighting the challenges that arise when working with each of them. Show how factors such as precision, consistency, and durability can be particularly challenging to achieve in this field. Use contrasting colors and textures to create a sense of tension and contrast within the image.
Key Takeaways
Recognizing the critical impact of global supply chain disruptions on the metal fabrication sector.
Importance of addressing skilled labor shortages to sustain industry resilience and growth.
Understanding the imperative to balance rising production costs with customer expectations.
Exploring innovative strategies and technology solutions for resolving challenges in metal fabrication.
The role of ERP systems and CAD integration in enhancing operational efficiency and productivity.
Emphasizing the necessity of training initiatives to bridge the technical skills gap within the industry.
Surviving a Volatile Raw Materials Market
In my experience within the metal fabrication industry, adapting to the ever-shifting market dynamics, especially regarding the supply of raw materials, is crucial for maintaining business continuity. Recognizing the raw material pricing volatility is a step forward in crafting robust procurement strategies that safeguard operations against unpredictable changes.
Each day, the London Metals Exchange influences the ebb and flow of metal prices globally, which has a profound impact on steel production costs. China's predominance in stainless steel and steel manufacturing also adds layers of complexity in quality and financial forecasting, pushing us to reevaluate our supply chain design for enhanced resilience and efficiency.
Impact of Global Supply Chain on Metal Pricing
The global supply network, while expansive and interconnected, often faces disruptions that can lead to increased costs and extended lead times. This necessitates a strategic approach to managing the supply of raw materials with an eye on the commodities market and London Metals Exchange trends.
Strategies for Achieving Optimum Inventory Levels
To combat the challenges associated with materials sourcing, I've found leveraging integrated ERP solutions to be indispensable. They offer supply chain visibility, enabling us to achieve optimum inventory levels through informed decision-making while also accommodating sudden shifts in market demand and pricing.
Employing advanced ERP systems supports our procurement strategies by managing the financial risks associated with raw material pricing volatility. It arms us with essential insights to remain proactive rather than reactive—anticipating stock shortages and capturing price fluctuations for better budget control and accurate quoting.
Journeying through the intricacies of metal market fluctuations, it's evident that knowledge and strategy are our best allies. By embracing modern technology and staying informed about market forces, we position ourselves not merely to survive but to thrive amid the uncertainties of a volatile raw materials market.
Streamlining Customization in Metal Fabrication
In my role as a metal fabricator, I have encountered a multitude of unique customer requirements, which have pushed my craft towards more custom manufacturing approaches. I've learned that maintaining flexible processes is essential, allowing us to adjust seamlessly to design changes, sometimes even mid-production. This agility is crucial in delivering tailor-made solutions that epitomize product customization.
The synergy of CAD integration with our ERP system is a cornerstone of our ability to meet these customization challenges. Through this harmonization, I can ensure that any adjustments in design are immediately reflected across the entire production cycle, leading to more accurate cost estimates and a robust fulfillment of our customers' complex needs. Such operational efficiency is not a happy accident but the result of streamlined processes and cutting-edge technology.
Employing advanced CAD software to translate detailed customer designs into actionable production plans
Integrating these plans with an ERP system for real-time updates and adjustments
Enabling a responsive production environment that can pivot as per customer demand
Below is a look at how CAD and ERP integration contributes to our operational efficiency:
Production Phase | Without Integration | With CAD Integration |
---|---|---|
Design Transmission | Manual entry, prone to error and delays | Automatic, immediate, and precise |
Cost Estimation | Estimations often inaccurate due to manual calculations | Real-time data leads to precise and reliable cost forecasting |
Production Adaptability | Slow to respond to design changes | Agile, accommodating rapid alterations |
Customer Satisfaction | Variable, dependent on the manual process success rate | Enhanced, thanks to the accuracy and speed of fulfillment |
When I look at successful projects in my history of metal fabrication work, they are characterized by a shared attribute: the precision and fluid adaptation of smart manufacturing solutions. A project's success is often due to the harmonious blend of innovation with traditional craftsmanship—a recipe for excellence in the realm of custom manufacturing.
Adapting to the Skills Gap in Metalworking
As the phenomenon of the skills gap in metalworking continues to expand, the industry is reaching a critical juncture. The scarcity of qualified welders and technicians proficient in modern Manufacturing Operations Management (MOM) systems only underscores the urgency for impactful workforce development. No aspect of metalworking remains untouched by this issue, from foundry floors to the assembly lines that depend on labor efficiencies.
Technology's Role in Bridging the Training Divide
Addressing the disparity begins with the strategic application of technology. By integrating comprehensive ERP solutions into shop floor management, companies can enhance operations and provide real-time productivity feedback. This data is instrumental in directing where skills training programs are most acutely needed, allowing for a more focused and rapid upskilling environment.
Creating a Pipeline for Skilled Labor
Fostering a robust workforce development initiative is not just a strategic move—it's a necessity for future survival. I've witnessed firsthand how introducing hands-on training and apprenticeship programs can create a sustained talent pipeline, ensuring that the investment in newer, more complex systems pays off. These programs don't just produce workers; they forge would-be artisans adept in the technologies that will carry metalworking into the next generation.
Training Initiative | Goal | Outcome |
---|---|---|
Advanced Welding Programs | Develop skilled welders able to handle complex materials and techniques | Enhanced capability to address specialized welding tasks |
MOM Systems Workshops | Educate staff on navigating and maximizing the benefits of MOM software | Increased operational throughput and reduction in production discrepancies |
Apprenticeship Pathways | Bridge the skills gap with hands-on, mentor-guided training | Stream of qualified workers prepared for immediate entry into the workforce |
In conclusion, as we adapt to the ongoing skills challenges within metalworking, the importance of integrating technological solutions with hands-on, skills-focused training cannot be overstated. It's the blend of the old and the new—the traditional craft honed alongside cutting-edge systems—that will ensure the growth and sustainability of the metalworking sector.
Embracing Advanced Manufacturing Techniques
In my journey exploring the nuances of the metal fabrication industry, I’ve witnessed firsthand the transformative impact of advanced manufacturing techniques. By integrating these innovative practices, companies are not only optimizing plant production but are also unlocking the potential for customized part mass production without the corresponding increase in costs. This strategic shift is not optional but a necessary step towards securing a competitive advantage in an industry marked by rapid change and fierce global competition.
Implementing these technology solutions goes beyond mere adoption; it requires a cultural change within the organization where efficiency and continuous improvement become deeply ingrained. My conversations with industry leaders reveal a common thread: the need to leverage advanced techniques for plant production optimization, thereby ensuring operational agility and scalability in the face of demanding market dynamics.
Take the example of 3D printing, which is revolutionizing how we think about prototyping and production. By allowing for the rapid production of complex and tailored components, fabricators can reduce lead times and material waste. Similarly, robotic automation has been instrumental in repetitive tasks, improving precision and consistency, which are critical in achieving refined outputs in mass quantities.
3D Printing Technologies
CNC Machining Advancements
Robotics and Automated Systems
Smart Factory Initiatives
Real-time Data Analytics
While adopting these techniques requires substantial capital investment, the long-term benefits in terms of productivity and quality cannot be overstated. The goal of integrating these systems is to create a balanced ecosystem where speed, customization, and efficiency coexist, propelling metal fabrication shops toward plant production optimization and hence, sustainable growth.
I am convinced that as the industry continues to evolve, those who embrace the full spectrum of advanced manufacturing capabilities will lead the way in innovation and profitability. It's an exciting time to watch technology and manufacturing converge to redefine what's possible in metal fabrication.
Reducing Welding Spatter and Other Shop Floor Inefficiencies
My deep dive into the world of metal fabrication has revealed that a key to maximizing metalworking efficiency is to focus on reducing welding spatter. As someone committed to enhancing shop floor efficiencies, I've learned it's not just about doing things right; it's about doing the right things efficiently. Welding operations are fundamental to clean, efficient, and productive fabrication businesses.
Innovative Techniques for Cleaner Welding Operations
My exploration of welding processes highlighted the fact that clean welding operations start with precision and end with a meticulous finishing process. To significantly reduce welding spatter, I've found several innovative techniques that many fabricators swear by:
Pre-welding anti-spatter agents prevent spatter from adhering.
Advanced spatter control welding machines that offer better arc stability.
Optimized welding parameters that include voltage, current, and wire feed speed.
Lean Principles to Boost Shop Floor Efficiency
What truly sets a fabricator apart is their drive for efficiency, and lean manufacturing principles are at the core of this journey. By applying these principles, I've noticed a culture of continuous improvement that permeates the entire operation, from top to bottom:
Lean Principle | Application on Shop Floor | Impact |
---|---|---|
Value Stream Mapping | Analyzing workflows to identify value-added and non-value-added steps. | Minimizes waste, leading to faster and more predictable production cycles. |
5S (Sort, Set in order, Shine, Standardize, Sustain) | Cleaning and organizing the workspace. | Improves safety and workflow efficiency; reduces wasted time searching for tools. |
Kaizen (Continuous Improvement) | Regularly scheduled process assessments and improvements. | Encourages innovation and problem-solving at every level of the organization. |
Jidoka (Automation with a Human Touch) | Integrating smart welding equipment that can detect and prevent defects. | Increase in quality with reduced manual intervention, leading to higher customer satisfaction. |
Just-In-Time Production | Producing only what is needed, when it's needed, and in the amount needed. | Minimizes inventory costs, reduces space requirements, and cuts down lead time. |
Incorporating these principles has not just been about streamlining tasks and reducing overhead, but it has forged a pathway to a more sustainable, cost-effective, and efficient future in my metalworking endeavors. By putting an emphasis on lean manufacturing principles to refine our works, the byproduct is not just a more cohesive workshop but one that sets the standard for fabrication efficiency.
Mitigating the Impact of Energy Costs
As a metal fabricator, I've seen firsthand how rising energy costs can swiftly erode profit margins. To stay competitive while maintaining sustainable operations, we must adopt energy-efficient welding techniques and integrate eco-friendly manufacturing practices throughout our facility. By sharpening our focus on operational cost management, leveraging the latest technologies, and operational optimizations, we can steer our manufacturing plants toward a more cost-effective and environmentally responsible future.
One effective strategy is to assess and overhaul our welding operations. Traditional welding processes can be incredibly energy-intensive, but with newer technology, we have the ability to transition to more energy-efficient welding techniques that conserve electricity and reduce our carbon footprint. From variable frequency drives to advanced inverters, the tools at our disposal allow for precise control of the welding process, which translates to less energy waste and, by extension, lower bills.
Investing in high-quality welders and training staff on advanced techniques like pulsed welding can also contribute to our track record of eco-friendly manufacturing practices. A pulse welder can reduce the amount of heat and energy needed while improving the quality of the weld, thereby decreasing the likelihood of rework—another source of unnecessary energy usage and costs.
Apart from direct process improvements, it's crucial to explore external avenues for financial relief, such as government incentives. Programs that support sustainable operations often provide grants, tax benefits, or rebates to companies trying to go green. I'm committed to keeping abreast of these opportunities to ease the financial load on our operations.
The key is not to prioritize what's on your schedule, but to schedule your priorities, and energy efficiency is at the top of that list for any forward-thinking fabricator.
Curbing energy expenses is not out of reach; it simply requires an intelligent approach to operational cost management. By optimizing our equipment setup, scheduling preventative maintenance to avoid energy-draining breakdowns, and considering renewable energy sources, we build a robust infrastructure that withstands the tumult of fluctuating power costs.
Let's take a closer look at some of the steps we're already implementing to ensure our operations remain competitive and sustainable, despite the growing concern over energy expenditures:
Transitioning to LED lighting systems throughout the plant to decrease electricity usage
Implementing automated systems to power down machinery when not in use
Conducting regular energy audits to identify and mitigate inefficiencies
Exploring the possibility of solar panels or other renewable energy sources for on-site generation
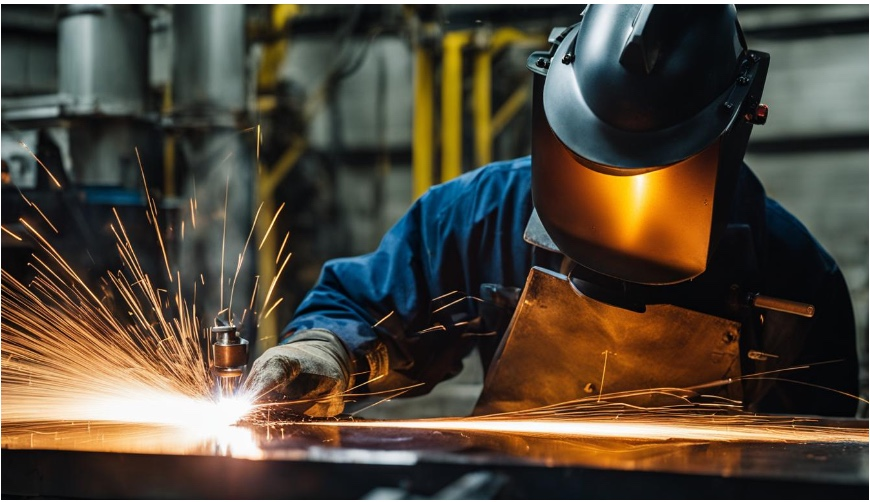
A welding machine emits minimal smoke and sparks while producing a seamless joint on a metal sheet in a factory setting. The lighting is dim, with glowing sparks illuminating the operator's face as they work. The background shows energy-efficient lighting and machinery in use.
As we strive to forge a sustainable, cost-effective path in metal fabrication, implementing these measures isn't just a means of navigating the challenges posed by rising energy costs; it is evidence of our commitment to innovation and our dedication to the principles of environmental stewardship.
Operational Challenges in Metal Fabrication
In my experience, the inexorable push for customization in metal fabrication paired with demands for speed in production presents a significant challenge in the sector. Enhancing manufacturing competitiveness requires a strategic approach to operational processes, particularly when it comes to the reduction of unproductive downtime and the maintenance of immaculate quality standards.
Addressing Customization and Speed Demands
The key to addressing the dual demands of customization and speed lies in the ability to swiftly adjust production processes to meet unique client specifications while adhering to aggressive timelines. Employing flexible manufacturing systems and lean methodologies has proven to be effective in my endeavor to meet these nigh-on conflicting requirements.
Integrating Predictive Maintenance and AI in Quality Control
Integrating predictive maintenance into our daily operations has been pivotal; it preempts equipment failures and directs maintenance efforts just before issues become critical. The convergence of this technique with the implementation of AI in quality control ensures a marked increase in efficiency and accuracy, aligning tightly with client demands without sacrificing speed.
The table below highlights improvements in efficiency after integrating predictive maintenance and AI into my workflow.
Parameter | Before Integration | After Integration |
---|---|---|
Downtime Reduction | 20% | 45% |
Error Rate in Quality Control | 5% | 1% |
Overall Equipment Effectiveness (OEE) | 65% | 85% |
Speed in Production | 80 units/hour | 120 units/hour |
Reducing Setup Time for Greater Competitiveness
As a professional in the field of metal fabrication, I've learned that reducing setup time is not just about shaving off a few minutes here and there; it's about revolutionizing the way we approach production to improve operational efficiency and maintain an edge in competitive metal fabrication processes. With ever-increasing market demands, I've seen firsthand the significant advantages of simplifying setups.
But what does 'setup time' really mean in our context? It refers to the period required to prepare machines and processes for the next production run. This interval can be constituted by various tasks such as adjusting tools, loading materials, and programming machinery—all of which need optimization.
To reduce setup times effectively, I advocate for several strategies:
Worker Training: Skilled workers who understand the intricacies of their machines can set them up more quickly.
Standardized Work: By developing standardized setup procedures, we minimize variations and inefficiencies.
Preventive Maintenance: Regular maintenance can prevent long downtimes due to machine failure.
The payoff for these efforts is substantial, not the least being the ability to offer customers faster turnaround times—a crucial differentiator in today's market.
Let me illustrate with an example. During my tenure at a leading fabrication facility, we reduced the setup time on our main press brake machine by 40%. How? We simply switched from manual tool setup to using a tool pre-setting station, significantly reducing the non-productive time. The impact on our overall efficiency was so profound that it reduced our lead times and bolstered our capacity to take on more projects.
The takeaway here is clear: lowering setup time propels us towards operational excellence, helping us meet deadlines, reduce backlogs, and, ultimately, satisfy our customers more consistently. In the relentless pursuit of operational efficiency, every second saved counts toward strengthening our hold in a competitive metalworking landscape.
Sustainable Operations: Beyond Recycling Scrap Metal
As an expert in metal fabrication, I've observed that sustainability is a multifaceted concept that starts with recycling scrap metal but doesn't end there. It extends into the very core of our production methods—the materials we choose and the processes we implement. By exploring sustainable materials in metalworking and applying comprehensive life cycle assessments to our products, we play a pivotal role in driving sustainable growth within the industry.
Using Sustainable Materials for Long-term Growth
In my journey toward more sustainable practices, I've embraced using sustainable materials. These materials, often made from recycled content or designed for easy recyclability, not only reduce waste but also conserve valuable resources. By selecting materials contributing to a more circular economy, metal fabricators like myself can support a long-term vision for growth that doesn't compromise the planet's health.
Implementing Life Cycle Assessment for Metal Products
Life cycle assessment (LCA) is a tool I use to measure the ecological footprint of metal products from the extraction of raw materials to their end-of-life. By quantifying the environmental impacts across the different stages of a product's life, I can identify opportunities for improvement. This might mean altering a design to reduce waste, adopting new technologies to lower energy consumption, or finding a second life for materials once considered scrap. Ultimately, LCA guides my decisions toward practices that nurture sustainable growth for the industry.
Committing to these sustainable operations is not solely about meeting regulations or market demands—it's about setting a new standard for the metal fabrication sector. It is my firm belief that this will not only preserve the environment for future generations but also ensure the longevity and success of our industry.
Incorporating Automation to Enhance Productivity
The paradigm of metal fabrication is shifting towards heightened automation in productivity. As I delve into the implementation of advanced systems, it's clear that integrating technology not only propels production but also dramatically elevates operational efficiency in metalworking.
Automating Repetitive Tasks for Operational Efficiency
My focus on automating repetitive tasks has underscored its crucial role in streamlining processes. Whether it's the precise placement of components or the meticulous timing of operations, automation redefines the metalworking landscape. Implementing such systems mitigates human error and frees skilled workers to focus on more complex tasks, a clear testament to operational advancement.
Industrial Robots: The Metalworking Game Changers
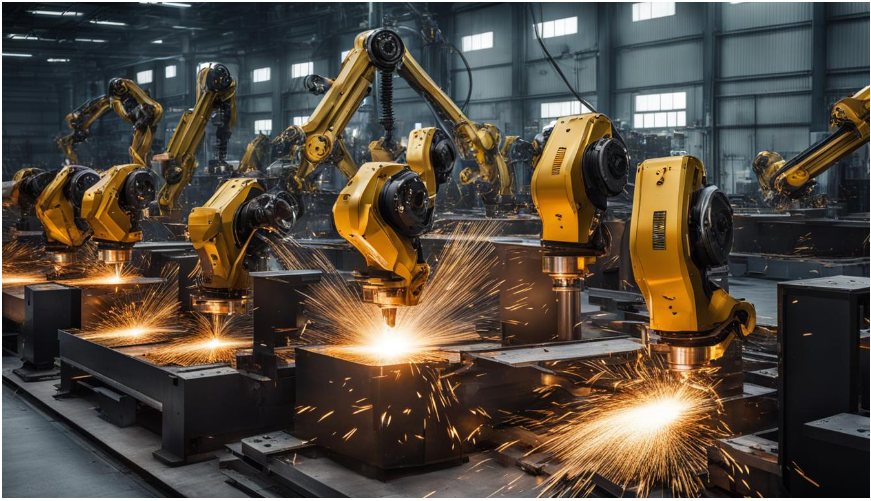
A cluster of industrial robots working efficiently in a metal fabrication plant, producing perfectly cut sheet metal and shaped metal pieces with precision and speed. The robots are programmed to work in unison, with their mechanical arms moving in perfect synchrony, showcasing the power of automation in enhancing productivity in metal fabrication. There is a sense of controlled chaos as sparks fly and machinery hums, creating a dynamic and energetic atmosphere that speaks to the modernization and innovation of incorporating automation into this industry.
In my recent tours of advanced metalworking facilities, the deployment of industrial robots for metalworking has been undeniably transformative. These robotic marvels excel in repetitive, high-precision tasks such as welding, cutting, bending, and even detailed painting, virtually reshaping the scope of what is achievable on the shop floor.
Task | Before Automation | After Automation |
---|---|---|
Material Handling | Time-consuming, Prone to error | Efficient, Accurate |
Machine Feeding | Manual, Labor-intensive | Automated, Cost-effective |
Welding Operations | Inconsistent quality | Uniform, High-quality |
Painting & Finishing | Varying standards | Precise, Aesthetic Excellence |
This is the era where industrial robots are not just assistants; they are game changers, reshaping the traditional boundaries of productivity. In my experience, their integration into modern metalworking protocols is a critical step in maintaining competitiveness in a fast-paced industry.
Conclusion
As we conclude this deep dive into the operational challenges plaguing the metal fabrication sector, my accumulated experience underscores the pressing need for effective solutions to steer this critical industry toward resilience and sustained growth. In my journey with Axis Solutions, I have seen firsthand how the right strategic approach can transform these challenges into opportunities for innovation and competitive differentiation.
Consolidating Strategies for Overcoming Fabrication Challenges
Through strategic investments in technology and initiatives aimed at workforce development, businesses within this industry can significantly enhance their process efficiency. By adopting cutting-edge solutions for operational challenges in metal fabrication, companies can manage not just the complexities of raw material pricing but also the ever-increasing customization demands that are now the norm in our sector. Furthermore, nurturing a skilled workforce is indispensable in addressing the pronounced skills gap while simultaneously elevating the expertise, quality, and precision of the work being accomplished on the shop floor.
Synopsis: Driving Towards a More Resilient Metal Fabrication Industry
My approach advocates for a comprehensive strategy that integrates sustainable practices into all facets of operation, from procurement to production. This will not only counteract existing limitations but also chart a course towards a more robust and adaptive metal fabrication industry. By embracing this strategic approach to metal fabrication challenges, we lay the groundwork for an industry that is not just surviving the demands of today but is poised to thrive in the face of tomorrow's uncertainties.